Licensing in Select International Markets
LaserBond systems have been engineered to get you started quicker without the need for specialist trained technicians.
Machine operators without specialised training can operate our Laser Cladding systems.
Our control system contains custom pattern files developed over many years, seamlessly integrated with our industrial robots to enable a near infinite range of parts and coating to be processed.
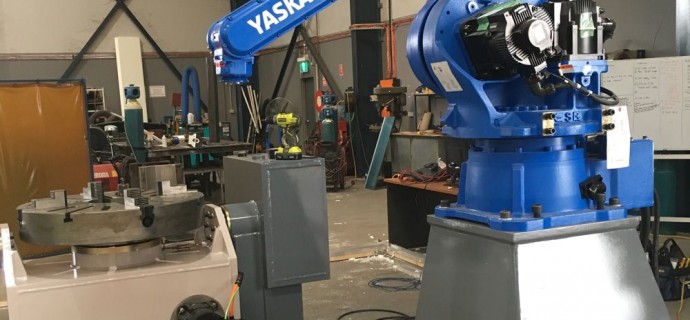
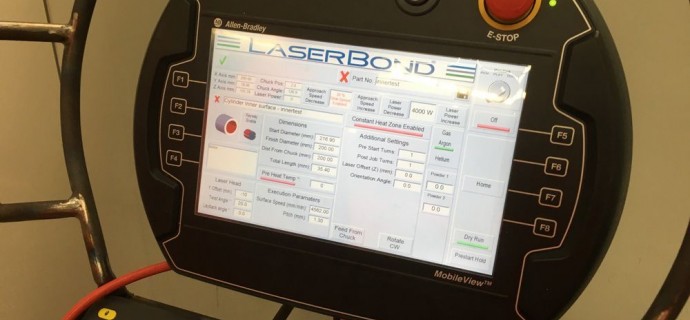

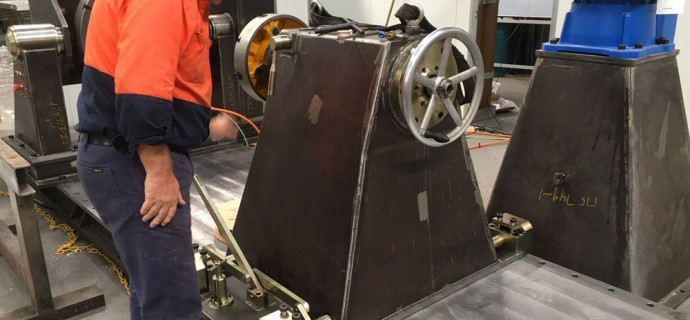
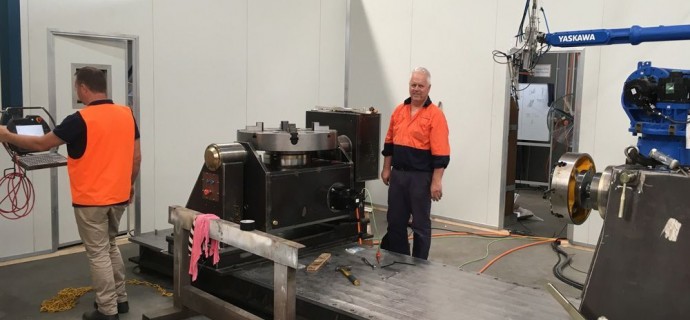
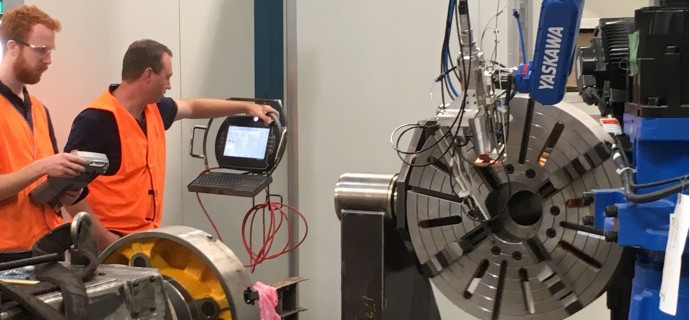
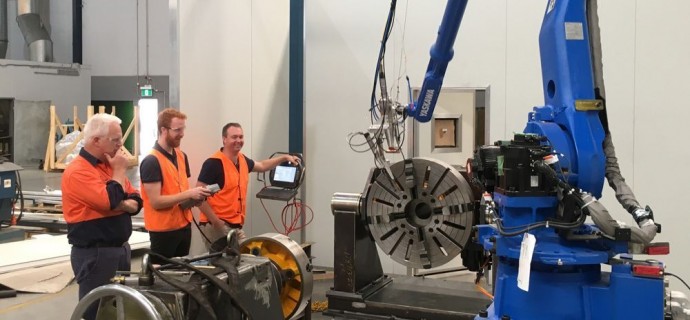
Operators do not need extensive or specialised training to operate the cladding systems. Our process and system knowledge are encapsulated in the control system and through our close application support.
Our systems are modular and scalable to your needs. Systems can be expanded using the core equipment, as your business and capabilities grow.
We offer our unique surface engineering technologies, hardware and training available for licensing in select international markets.
With 25 years of research, development and practical applications experience across a range of industry sectors – including mining, drilling, mineral processing, power generation, transport and marine, plant and machinery, manufacturing (including aluminium and chemicals), fluid handling and agriculture – the full suite of LaserBond wear resistant process engineering is a strong and viable investment.
Since 1994 we have been an innovator, firstly in thermal spray HP-HVOF systems, and now with our advanced additive Laser Cladding systems, which are custom designed for client applications. Our export systems are available in 4kW to 10kW laser power. Our largest integrated workpiece manipulation system is capable of 10 tonne components, 1.6m in diameter and 5.5m long.
The integration of laser robotics and workpiece manipulator enables complex shapes to be clad. Our unique water-cooled, off-axis powder injection nozzle incorporates a rapidly replaceable powder injection tube and gas depressurized gravity-fed powder mixer to manage the intense heat accumulating in the laser head. This allows high duty cycle production at maximum power levels.
To enable more complex geometry to be processed, we developed new control logic which runs on a PLC. Our R&D team have been developing and commercialising new laser processes and wear resistant materials for many years; our early work on Laser Cladding dates back to 1999 when we began building our own LaserBond® Laser Cladding system.
In 2014, our team lodged international patent applications for a new LaserBond deposition method that enables extremely thin layers of metallurgically bonded cladding to be laid down at low heat without inter-metallic dilution or porosity. In 2017, further patents are pending for a number of features of our new advanced manufacturing Laser Cladding cell.
许可
The LaserBond licensing package on offer integrates a tailored equipment package for an industry or market application with exclusive access to LaserBond surface engineering research and technology.
Packages include regular updates on new and/or improved cladding materials and techniques, a range of specialist technology, hardware and equipment with full off-site training. With each installation, LaserBond engineers and technicians do on-site commissioning and further application training.
A LaserBond ‘Technology Package’ enables our customers to become productive, making money, far faster than retracing the buy the hardware – integrate the components – develop the software systems – learn to operate the system – understand the metallurgy – build the QA process – and many more experience steps that LaserBond learned over time.
Specialised & Integrated Equipment Package
Depending on the intended industry application, specialist equipment in the integrated equipment package may include:
- HP HVOF (High Pressure High Velocity Oxygen Feed) application station
- Advanced Additive Manufacturing Laser Cladding station
- Multi-axis robot control of the cladding head
- Task oriented parts handling system
- Consumable feeders
- Control systems
The assembly and integration of individual components takes place at a LaserBond facility, where systems are tested, calibrated and prepared for the owner. Customer training takes place on their own equipment.
After training, the equipment is disassembled and packaged for shipping. We recommend the owner’s technician be part of the process as a further training exercise.
LaserBond technicians are also on the customer’s site for final installation and commissioning.
Owner & Operator Training
Owner and operator pre-training is undertaken at a LaserBond facility with a comprehensive staged operator training program designed to develop competent and proficient operators to work with a range of LaserBond Surface Engineered Cladding processes.
The modules included in the training program cover Preparatory Machining, Thermal Spraying, Laser Cladding, Surface Finishing, Robotics Programming and Surface Coating Tribology and Metallurgy. Each module is available in four skill levels with unique competency-based outcomes.
Ongoing System & Business Support
LaserBond has a wide range of experience across many industries. Our R&D technicians have developed robust solutions for hundreds of different technical and commercial wear problems.
A licensee can access ongoing support for their system troubleshooting online for maintenance and other technical issues. Access is also available to our R&D team and their surface engineering laboratory, to assist with application issues involving both methodology and metallurgy.
Fast-start Tailored Solutions
LaserBond surface engineering technologies and processes provide industrial customers extended wear life and significantly reduced overall operating costs. An extensive R&D program is developing new and innovative surface engineering applications to increase the advantages we offer our customers.
Your interest is invited. Please contact LaserBond.