LaserBond is a classic grass roots family founded business.

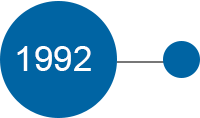
Gregory Hooper while working as a leading technical specialist in welding applications and metallurgy foresaw a services company that could embrace new metal spray deposition technology. With family support, Greg founded the company as HVOF Australia P/L in 1992, working from a small workshop in Ingleburn, NSW.
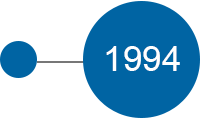
His brother, Wayne Hooper joined the business in 1994.
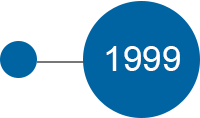
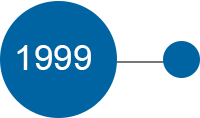
Our innovation with Laser Cladding dates back to 1999, when we commenced the design of one of the world’s first high-powered Laser Cladding system (6kw). This cell has been in operation since 2001.
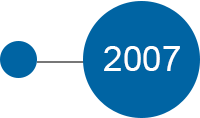
ASX listed as LaserBond Limited (ASX:LBL) in 2007.
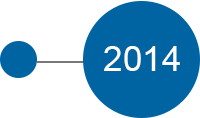
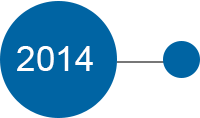
In 2014 our team lodged patent applications for a revolutionary new “LaserBond deposition method” that enables extremely thin layers of metallurgically bonded cladding to be laid down at low heat without inter-metallic dilution or porosity.
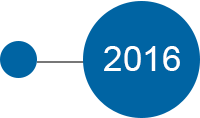
LaserBond has now built several laser systems, the latest one is a 16kw unit integrated into an advanced robotic manufacturing cell.
Family Founded in 1992
LaserBond is a classic grass roots family founded business. Gregory Hooper while working as a leading technical specialist in welding applications and metallurgy foresaw a services company that could embrace new metal spray deposition technology. With family support, Greg founded the company as HVOF Australia P/Lin 1992, working from a small workshop in Ingleburn, NSW. His brother, Wayne Hooper joined the business in 1994.
Relocating to a larger premises in Smeaton Grange, NSW in 2014. Cavan, SA was established in 2012 and was ASX listed as LaserBond Limited (ASX:LBL).
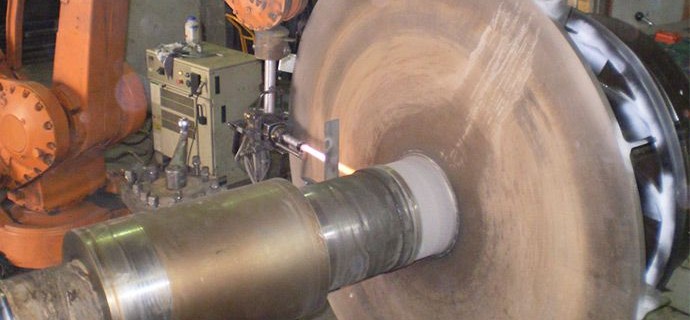
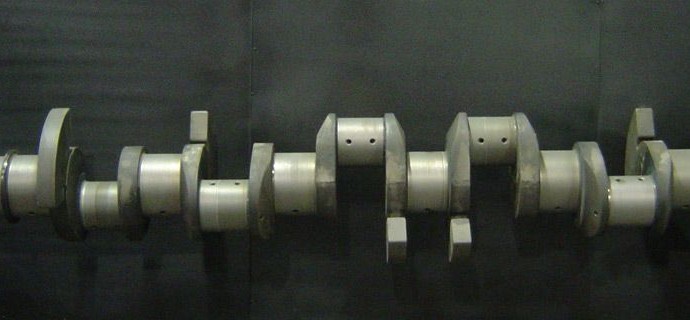
Innovation Led Growth
The company was at the forefront of the development of the High-Pressure High Velocity Oxy Fuel (HP HVOF) process. The HP HVOF process sprays semi-molten droplets of coating material at extremely high velocities, resulting in coated surfaces of the highest possible quality and performance to improve durability, resistance to corrosion, or both. The investment in an in-house Scanning Electron Microscope remains unique today amongst LaserBond’s peers. The design and application required-performance metallurgical claddings requires an understanding of bonding and the deposited material. The well-equipped metallographic laboratory enabled LaserBond to make world-leading advances in surface engineering for wear.
Our innovation with Laser Cladding dates back to 1999, when we commenced designing one of the world’s first high-powered Laser Cladding system (6kw). The company now has built several laser systems, the latest one is a 16kw unit integrated into an advanced robotic manufacturing cell..
In 2014, our team lodged patent applications for a revolutionary new “LaserBond deposition method” that enables extremely thin layers of metallurgically bonded cladding to be laid down at low heat without inter-metallic dilution or porosity.
Industry Collaboration
LaserBond’s growth has accompanied its collaborative relationships with key and enduring customers. Starting from a problem-solving opportunity we develop technology-based solutions to wear life and performance problems that constrain our customers. In turn we develop specialised products, or standardised service protocols that becomes a growth partnership.
Our formal R&D collaboration with UniSA accelerates this passion for innovation.
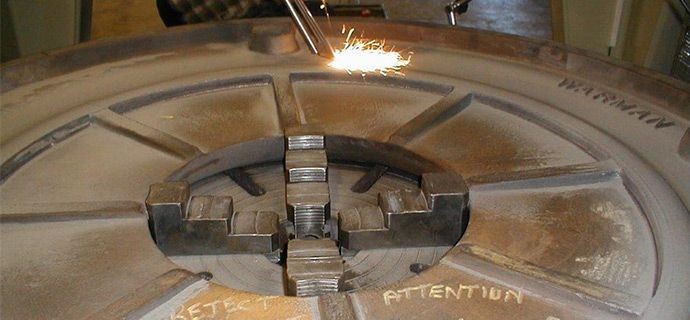