Mineral processing involves abrasion, corrosion and wear.
Slurry on screens, pumps, tanks, rakes, valves, centrifuge screens. Rock on sizers, crushers, rollers, idlers. If a part of the process fails through metal fatigue, wear or abrasive erosion, the whole process stops.
When applied to production-vital components, LaserBond surface engineering technologies – developed to improve availability and productivity by extending component life – increase resistance to wear and corrosion, optimise performance, extend plant and machinery operational life, increase reliability, reduce component change-outs, reduce downtime and reduce overall operating and maintenance costs.
And that will improve the process.
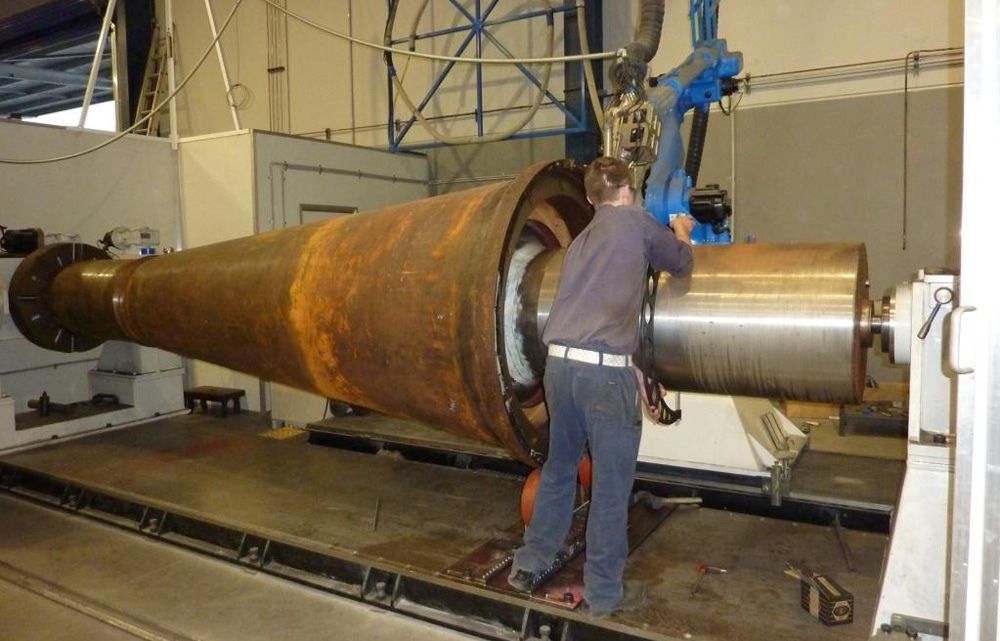
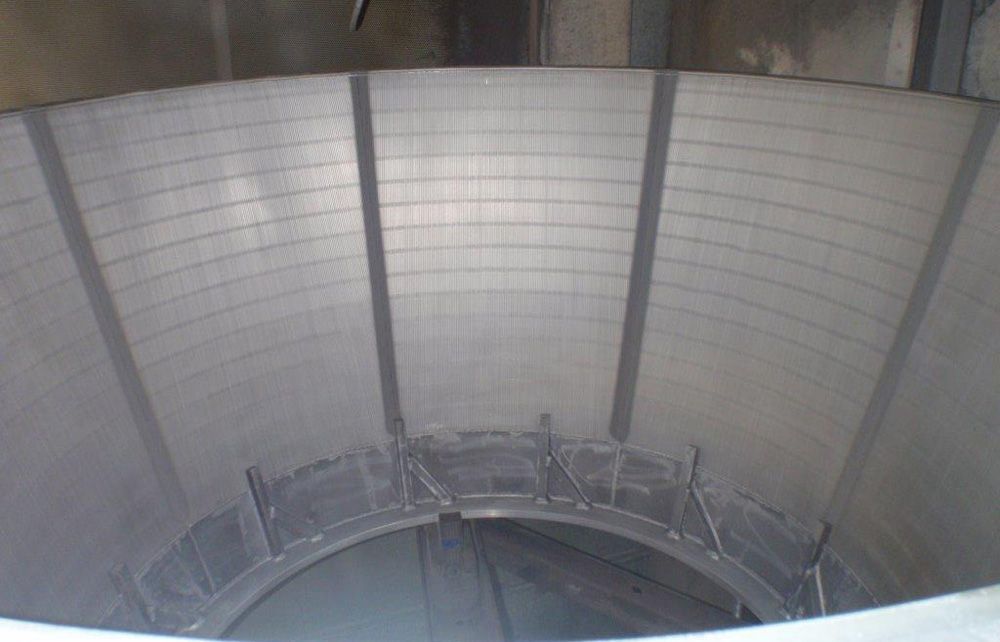
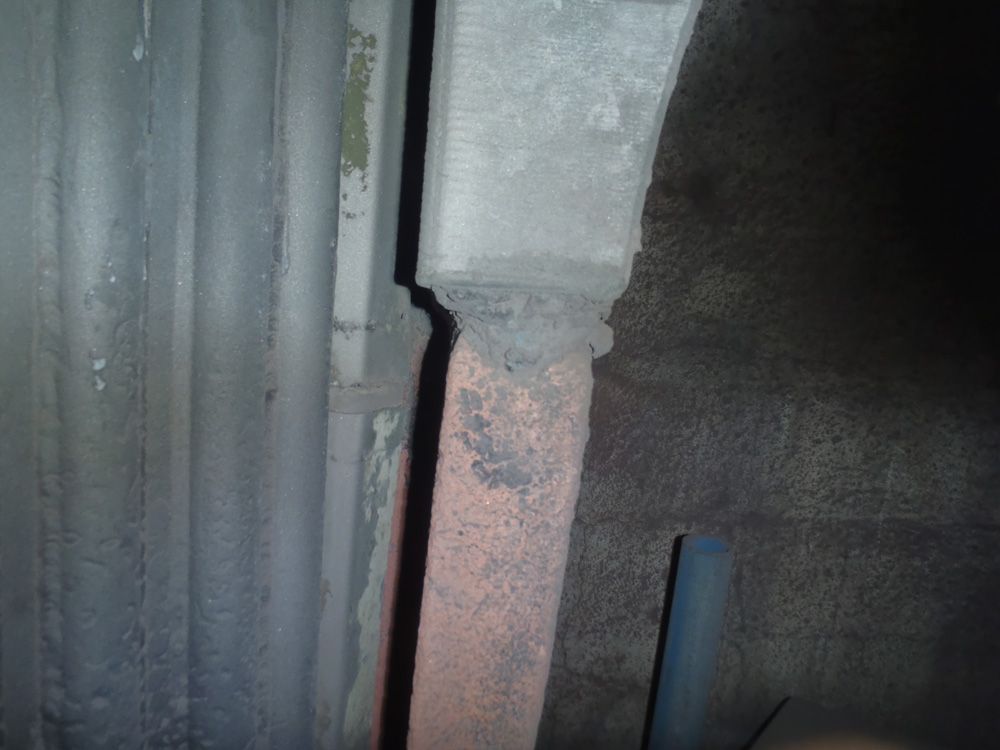
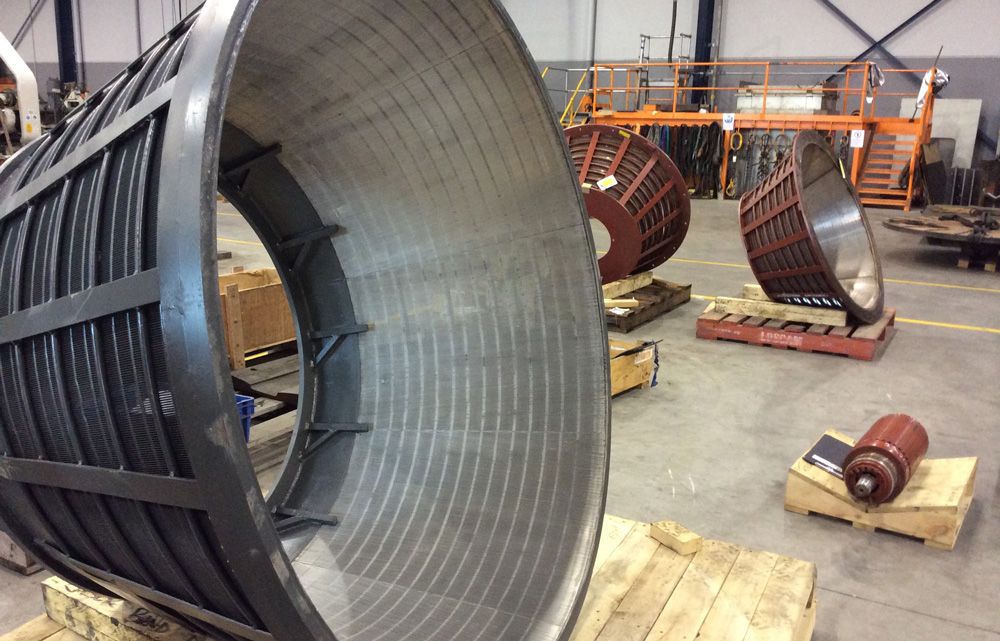
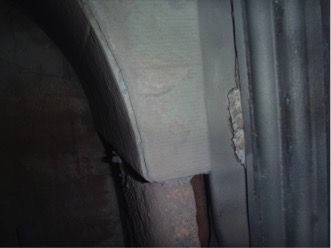
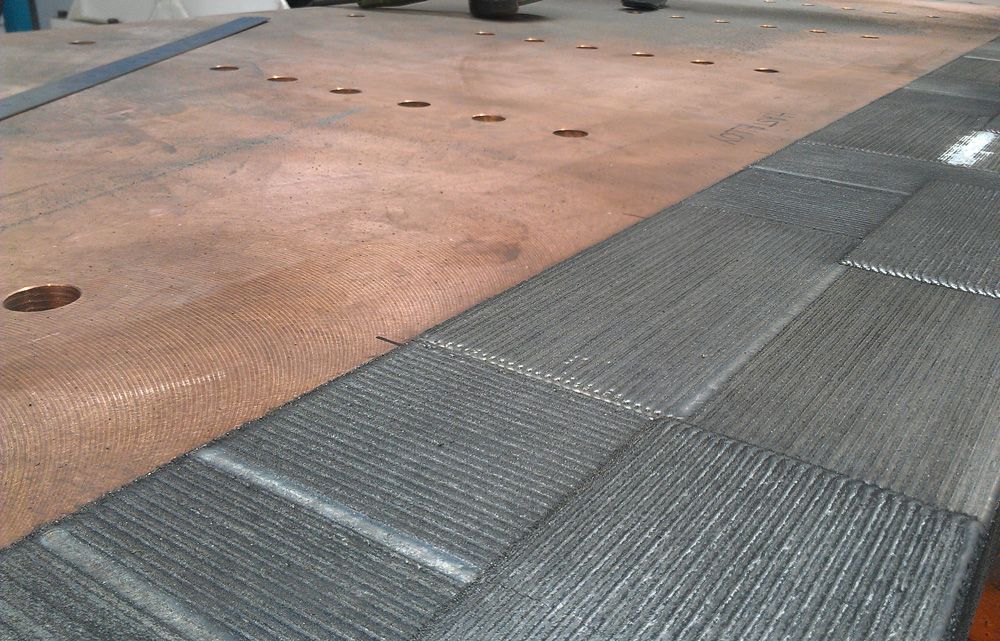
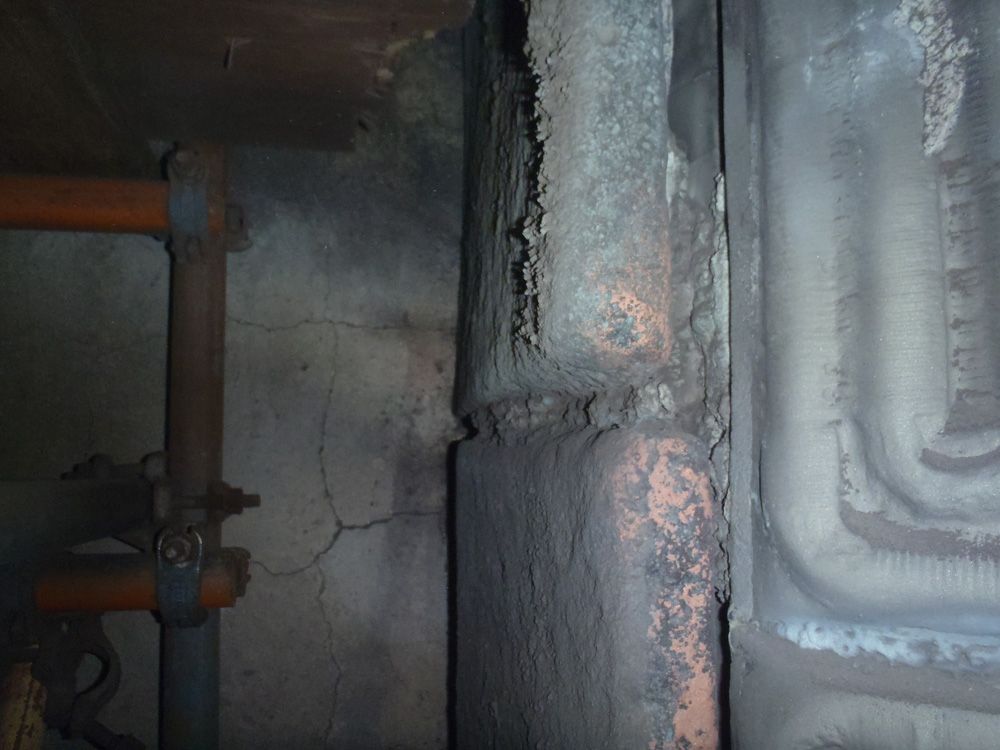
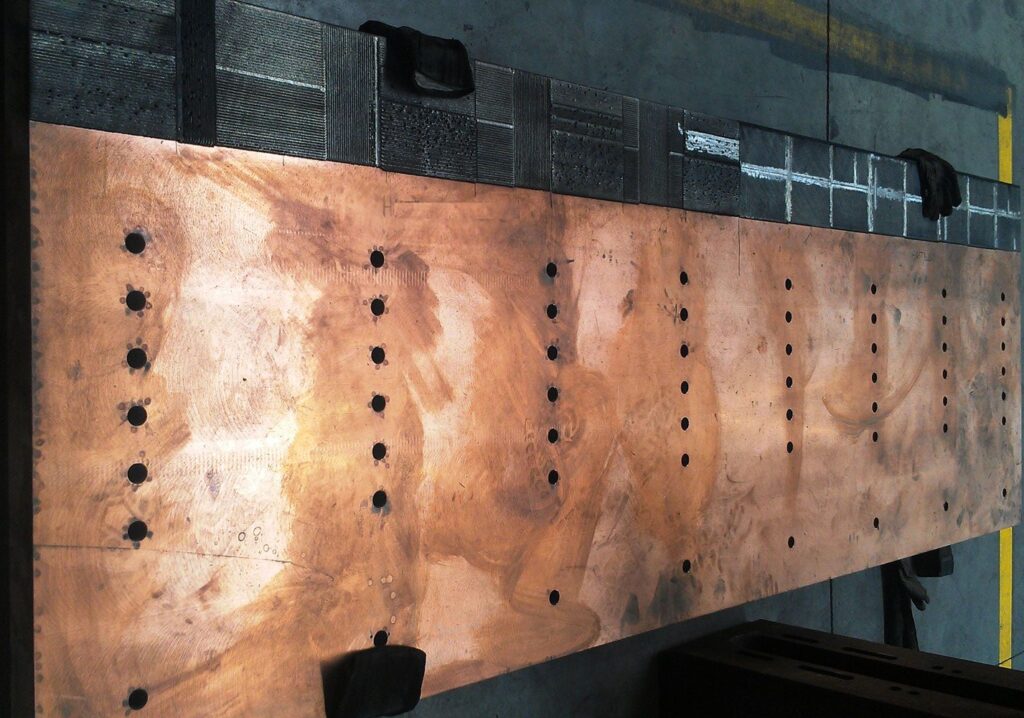
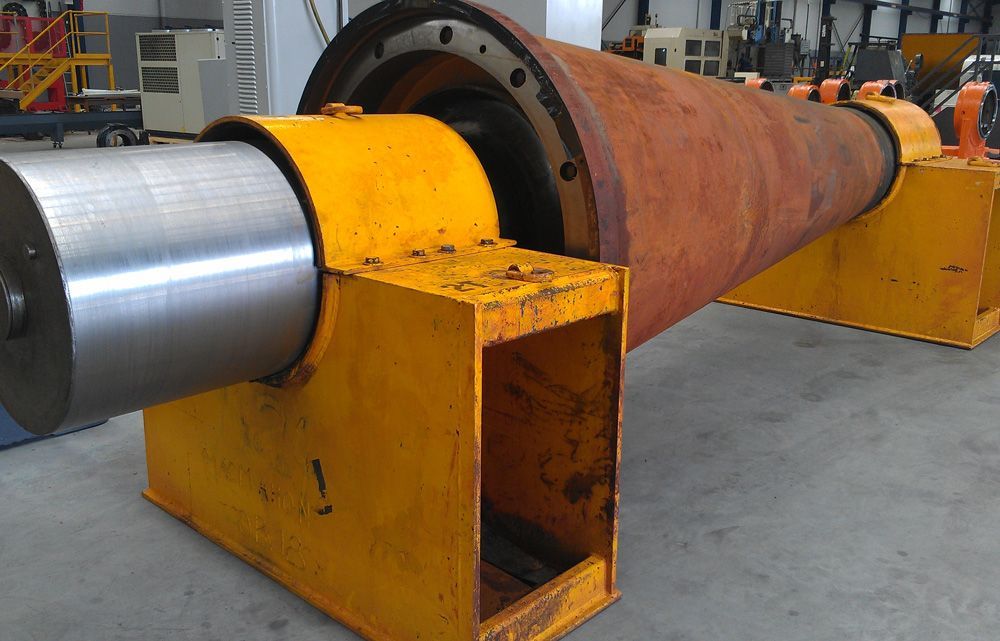
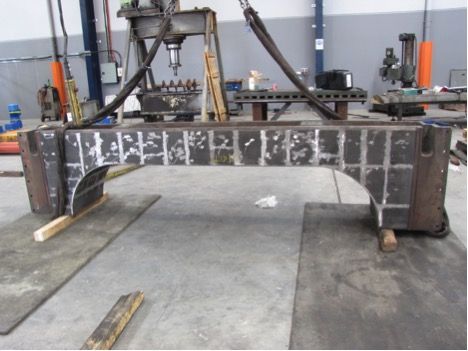
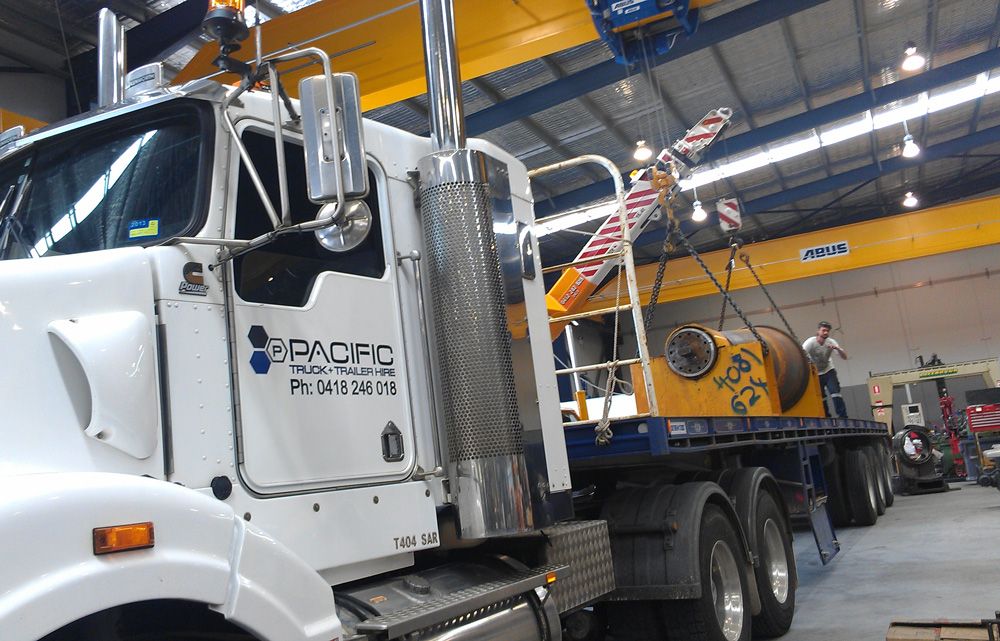
Benefits:
Extended Maintenance Cycles
Maintaining the process is maintaining output. LaserBond surface engineered wear-susceptible equipment and components will perform longer. The potential for part failure will be reduced. Breakdowns are reduced. And the maintenance cycle is extended.
Less Unscheduled Downtime
Component wear, metal fatigue and non-performing equipment ultimately need replacing. And that means unscheduled downtime. LaserBond’s technology extends the equipment lifespan and performance capabilities. Which means less unscheduled downtime.
Higher Process Yield
Processing equipment that operates and performs longer, smoother and better delivers benefits along the processing cycle. Less production interruptions, less equipment failures mean consistency. And that delivers a higher yield.
Case Studies
Our Stories… an enviable reputation built on solid performance.
Our client operates a poly-metallic underground mine in SA. The