Tribology is a branch of mechanical engineering and materials science
It is the science and engineering of interacting surfaces in relative motion and it has informed and influenced LaserBond’s R&D activities around the surface engineering technologies and techniques that make machinery and components perform better and last longer.
Surface engineering, to reduce common wear processes (corrosion, abrasion and erosion) and ultimately the total cost of ownership for users in capital intensive industries, is in our DNA.
We offer a range of coating materials, each one carefully matched to the characteristics of the job – the substrate, the process, wear patterns and the like – to enhance a component’s resistance to common wear practices.
Our range of coating materials includes;
- Nickel Alloys
- Cobalt Alloys
- Tungsten Carbide
- Ceramics
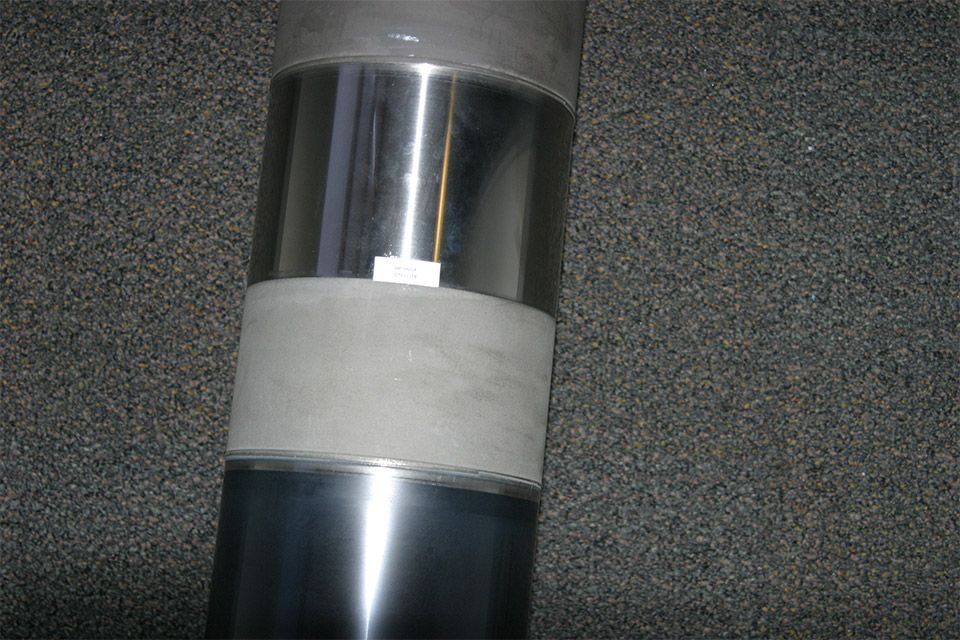
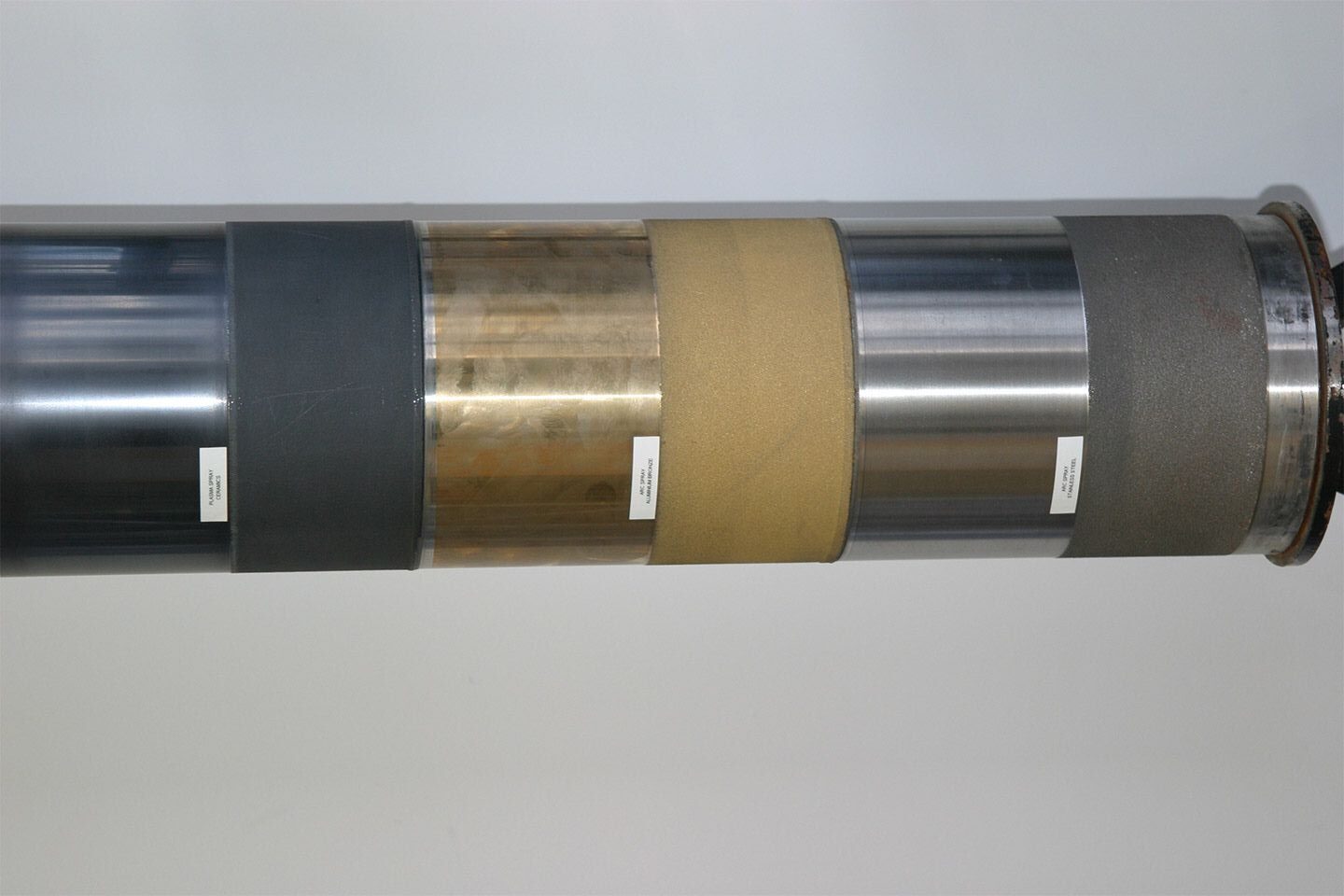
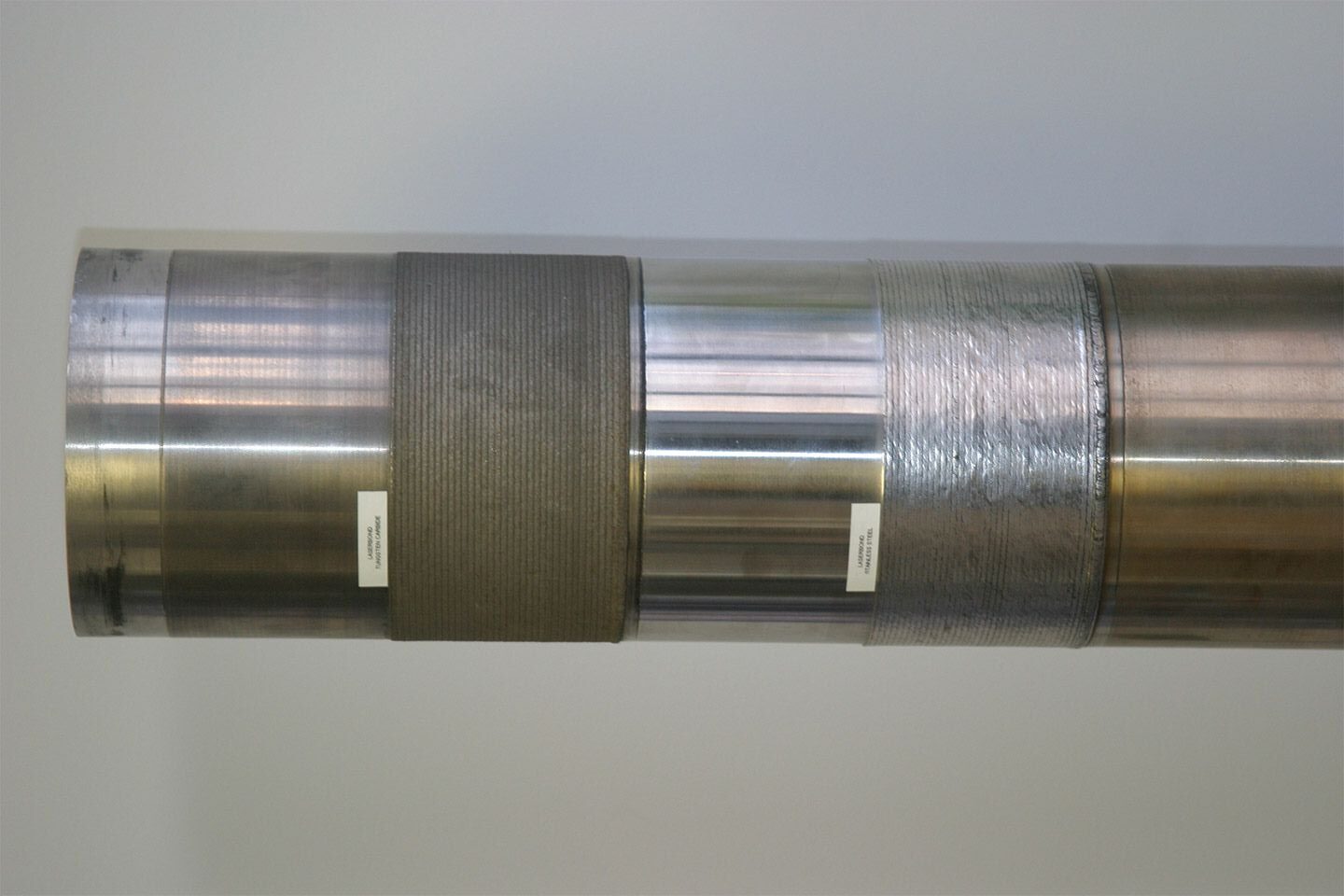
Nickel Alloys
Nickel is a versatile element and will alloy with most metals. Complete solid solubility exists between nickel and copper. Wide solubility ranges between iron, chromium, and nickel make possible many alloy combinations.
The major alloy types that are used are:
- Iron-Nickel-Chromium alloys
- Stainless Steels
- Copper-Nickel alloys and Nickel-Copper alloys
- Nickel-Chromium and Nickel-Chromium-Iron alloys
- Low Expansion Alloys
Applications and Characteristics of Nickel Alloys
Nickel and nickel alloys are used for a wide variety of applications, the majority of which involve corrosion resistance and/or heat resistance.
Some of these include:
- Chemical and petrochemical industries
- Aircraft gas turbines
- Steam turbine power plants
- Medical applications
A number of other applications for nickel alloys involve the unique physical properties of special-purpose nickel-base or high-nickel alloys.
These include:
- Low-expansion alloys
- Electrical resistance alloys
- Soft magnetic alloys
- Shape memory alloys
- Magnetic Alloys
Cobalt Alloys
A non-ferrous alloy, cobalt alloys are used for components and equipment requiring corrosion resistance and wear resistance at elevated temperatures.
Suitable to be applied by either thermal spray or laser cladding process, cobalt alloys provide anti-galling protection and provide extended wear through their exceptional hardness and toughness characteristics. They have extremely high melting points due to the cobalt and chromium content.
Particularly successful in the power generation sector, cobalt alloys are also protecting vital equipment such as valves and valve seats and diesel engine components.
Tungsten Carbides
Extremely hard and very resistant to heat and abrasion, tungsten carbide is the optimum coating for industrial machinery, tools and equipment used in the processing of carbon steels and stainless steel.
Applied at high temperatures, using thermal spraying technologies such as HP HVOF or plasma-arc, tungsten carbide provides a robust, super strong coating that is around twice the stiffness of steel to specialised production equipment such as cutting tools. Tungsten carbide is also widely used in the rotating ball in the manufacture of ballpoint pens.
On equipment such as precision cutting blades, tungsten carbide maintains a sharp edge better than other surface treatments, produces a better finish on parts and is ideal in high quantity production runs where other tools would wear away quickly.
Tungsten carbide clad equipment is suitable for use in almost all manufacturing and processing facilities and plants. It is considered resistant to acids and susceptible to attack only from hydrofluoric acid/nitric acid mixtures above room temperature.
Ceramics
Generally applied to metal components to enhance their functionality, ceramic coatings are advanced materials systems that provide extended corrosion and wear resistance and have a significantly higher level of abrasion resistance.
Best suited to insulating equipment and components from considerable and sustained heat loadings (>1600oC/3000oF), they withstand chemical erosion that occurs in other materials subjected to acidic or caustic environments, harder, stronger in compression and have excellent electrical and thermal insulating properties.
In high-temperature manufacturing environments, such as hot forging, ceramic coating increases the operational lifespan of forging dies, allowing them to produce a greater number of manufactured components before wearing down.
Ceramic coatings can be surface-finished to achieve required tolerances while maintaining high levels of resistance to wear, corrosion and mechanical erosion. They are ideal to create a thermal barrier between operating components in industrial and manufacturing facilities.