About Laser Cladding
LaserBond® Laser Cladding, also called Laser Metal Deposition (LMD) is a high performance additive manufacturing procedure which utilises precisely-controlled energy from a high power laser to metallurgically-bond a surfacing material to a substrate to provide very high performance surfaces to new parts for extended operating life. With this precise control, a welded or metallurgical bond is achieved with minimal impacts and effects of heat on both the substrate and surface material.
LaserBond® Laser Cladding technologies offer a broad spectrum of industries confronting component and equipment wear issues significant opportunities to reduce maintenance costs and enhance operating performance.
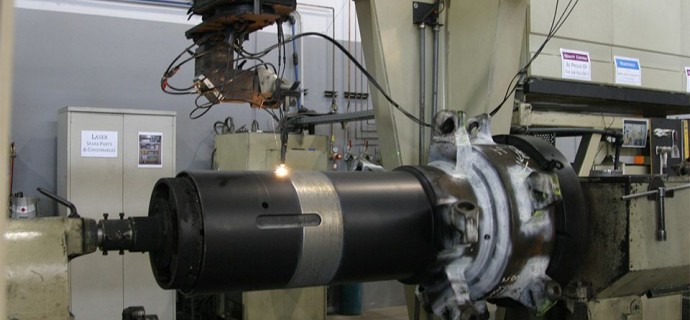
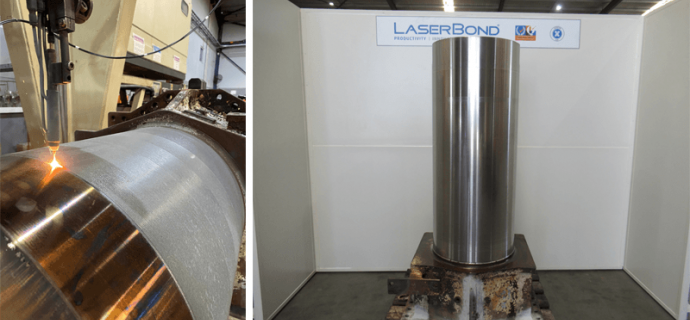
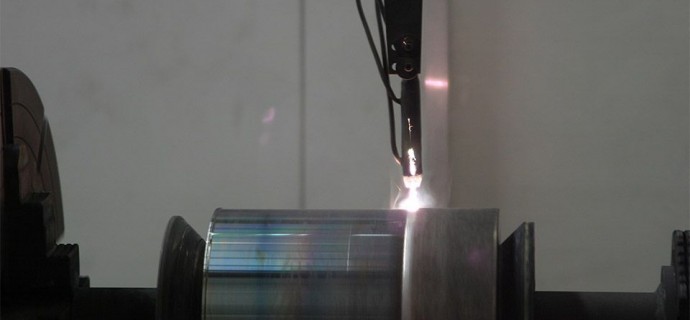
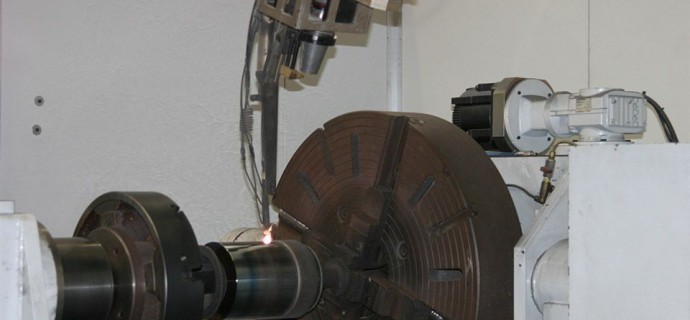
Benefits:
- Limited dilution of coating for maximum purity and performance
- Precise, fully-fused deposit layer
- Short processing time minimises heat spread and impact
- Improves component wear performance
- Cost effective component life extension
- Can be used to reclaim worn or fatigued components
- Reduces maintenance and part replacement costs
- Suitable for sensitive components
Applications:
- High erosion from liquid or gas flows
- High impact conditions
- Part-to-part wear and abrasion