Applying our DNA - Innovation Projects
LaserBond’s DNA lies in surface engineering innovation. Our best work comes from working in collaboration with our customers to solve recurring wear life performance problems.
Our R&D work is directed to three areas:
- Tribology – mechanics of wear
- Materials Science – powdered metals
- Additive Manufacturing Applications
We work in several high-growth industrial sectors where productivity improvement and reliable operations is a driving strategy – METS; Oil, Gas & Energy; Agriculture; Defence; Infrastructure. Some examples of collaborations projects follow:
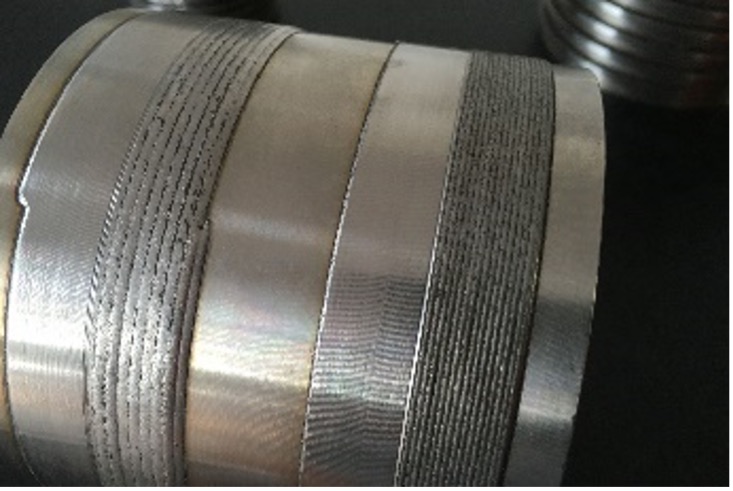
New (Cladding) Application - Hydraulic Cylinder Refurbishment
Hard chrome is a long-standing method of providing corrosion resistant and high-polished surfaces on hydraulic cylinders, however a hard-chrome finish does not perform well in high impact environments and has recognised environmental issues. To meet the challenge of finding a comparable, high-polish and hard-wearing finish, LaserBond developed a new, more efficient laser cladding process with metallurgy that is proving a superior and more economical replacement.
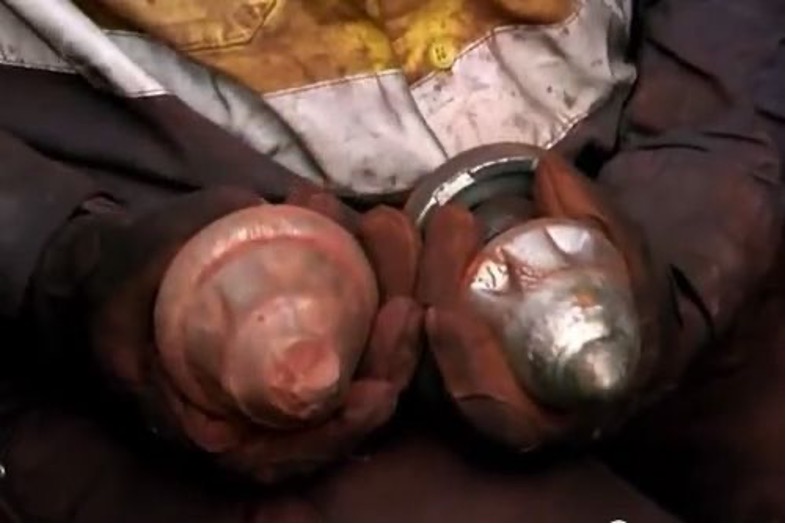
Understanding Wear Mechanics – Mining Picks
Efficient mechanical mining processes are driven by the wear-life of ground engaging tools – in part the consumable cost, and mostly the downtime to change them. To optimise productivity, these tools need the protection of tough, wear-resistant surface engineering technology. By taking a ‘whole problem’ approach LaserBond can develop a class of surface-engineered mining picks which incorporates our patented cladding technology to cut rock faster – and for longer.
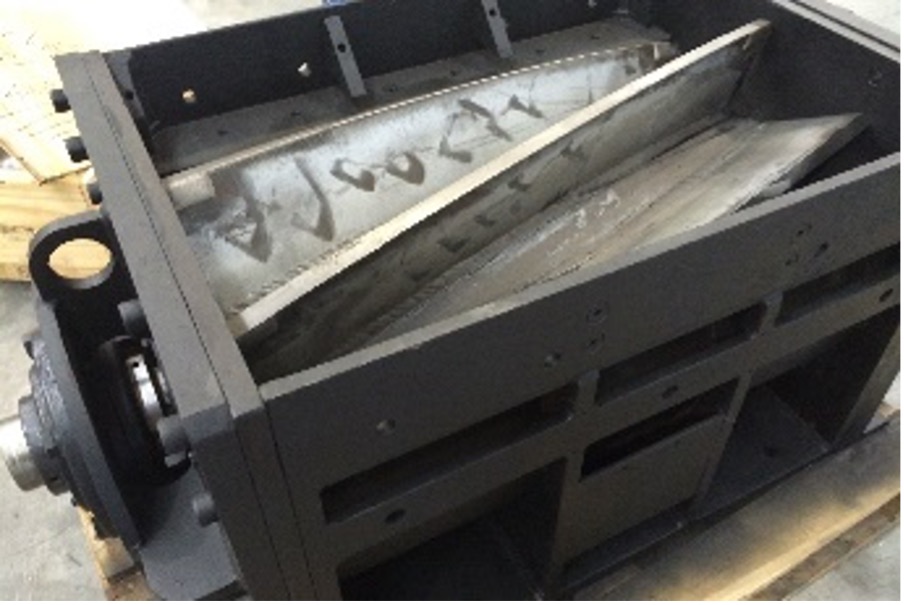
New Metallurgy – Bark Blower Reengineered for Stones
At LaserBond we understand the cause, not only the effect, of surface wear. What makes some metals and surfaces more susceptible to wear than others? What is the cause behind the effect? Components in high-temperature, high-load operating environments can face extremes of mechanical stress. OEMs account for these extremes when designing equipment but ultimately wear and physical erosion – and potential component failure – will be experienced. We have applied the metallurgical knowledge of more than 20 years of surface engineering experience to remanufacture heavy-duty drive units for off-road haul trucks – to keep them moving and productive.

New Methods – High Performance Wear plate
Typical wear plates used in mining applications are made from carbon-based alloy steels, heat treated often with some form of surface treatment to increase wear resistance. The higher performing specialised plates are made with a layer of chrome or tungsten carbide applied using automatic welding processes. LaserBond’s engineers recognised that there were several debilitating process characteristics related to the material dilution and heat stress affects that limit the in-service performance of the wear plate. Using a new multi-step process unique to LaserBond, we have developed wear plates with 11 times the wear life of competitive CCS units.
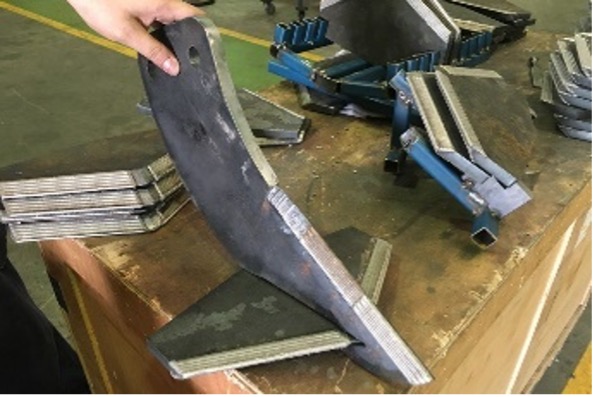
New Industries – Superior Ground Engagement Tools
West and South Australian farming soils are particularly sandy, which leads to aggressive wear rates of GET cutting edges. Worn tools leads to lack of soil penetration, or a breaking moisture layer. It leads to trade off better fuel burn, time and ultimately crop yield. LaserBond is working with machinery importers to develop higher performance self-sharpening GET.
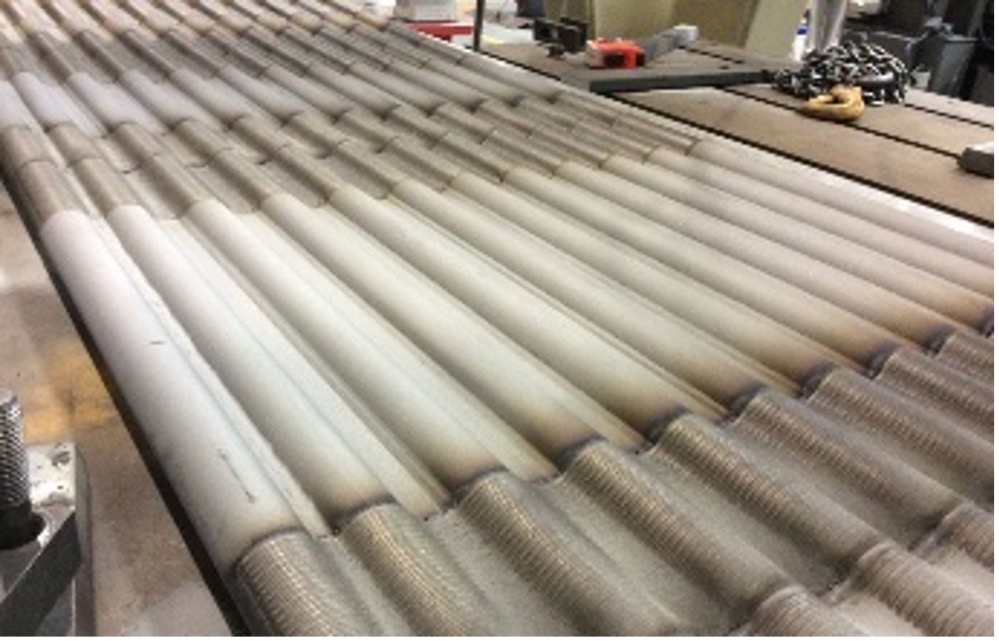
Enabling Technologies – Cladding of Boiler Tubes
Domestic and industrial waste streams are often directed to boilers for electricity generation, sugar mills burn particulate laden biomass (bagasse) fuel. Unlike other fuels, they contain a wide range of materials that damage boilers and are very difficult to remove; for example, PVC plastics create hydrochloric acidic gas when burnt; sand and other non-flammable ash erodes machinery. High pressure boiler tubes are damaged and leads to premature failure. LaserBond engineers are developing a suite of enabling technologies that involves application method, cladding metallurgy and a fabrication process to make long-life tube panels for waste boilers.